Return on Investment: Predictive Maintenance in the Biopharma Industry
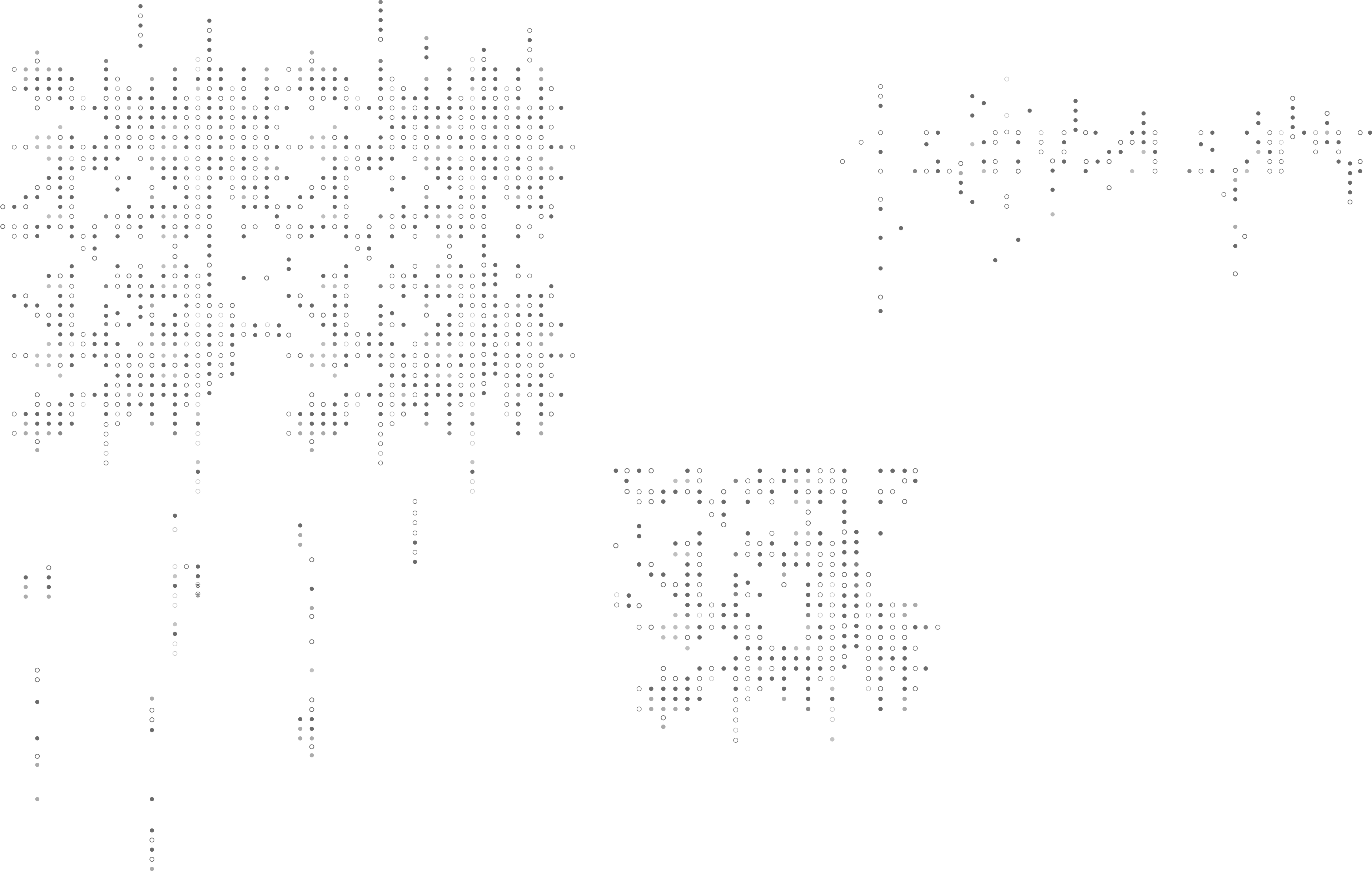
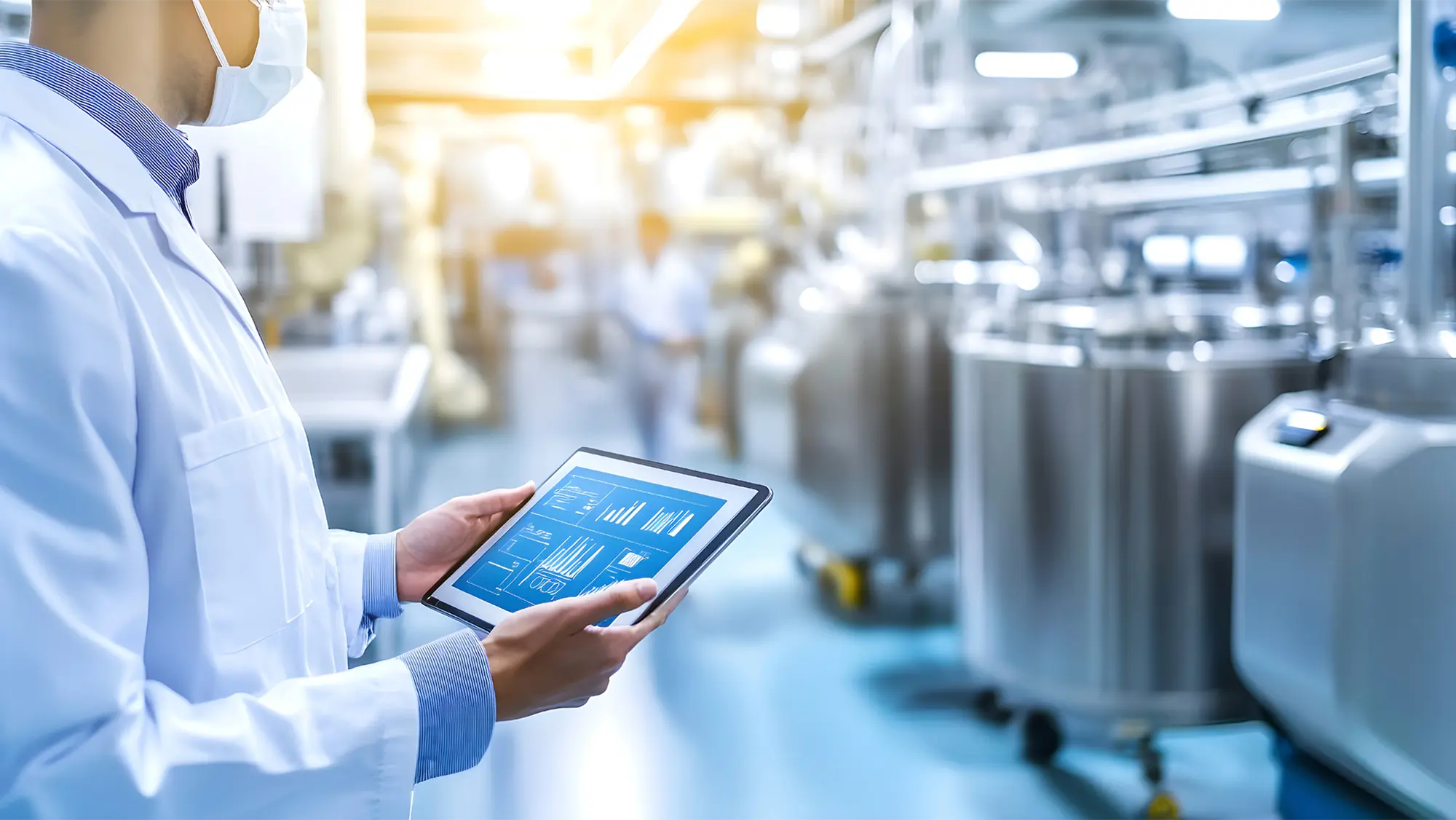
Unlock the ROI of Predictive Maintenance in Biopharma product storage
Facility managers and chief operating officers responsible for biopharma product storage are facing growing challenges to increase efficiencies, ensure compliance, and protect their valuable life-saving products — under critical timelines and budget constraints. Predictive maintenance tools, specifically designed for chamber applications, offer a data-driven, proactive approach to safely and confidently protect these irreplaceable assets. By diagnosing and preventing chamber failures before they occur, predictive maintenance platforms offer a significant ROI through cost savings, reduced downtime, and improved operational reliability.
This white paper provides insights as to how life sciences, biopharma, and research facilities can capitalize on predictive maintenance practices to streamline their storage operations, support their sustainability initiatives, and achieve measurable financial and operational benefits.
Your submission has been received!
Introduction
The pharmaceutical industry’s reliance on temperature controlled environmental chambers is essential — not just for compliance with stringent regulations but also for ensuring pharmaceutical product safety and efficacy. These chambers house valuable temperature-sensitive products such as pharmaceuticals, biologics, vaccines, orphan drugs, cell therapies, research materials, and patient samples which are susceptible to spoilage or degradation during chamber failures.
Unplanned chamber malfunctions can lead to compliance risks and operational disruptions that ultimately impact an organization’s bottom line. They can also result in massive product losses that directly affect patients. Traditional maintenance practices, whether reactive or preventive, lack the certainty needed to fully protect these invaluable and often irreplaceable products.
Enter predictive maintenance, which uses Industry4.0 technologies like advanced analytics, real-time monitoring, artificial intelligence and machine learning to take the uncertainty out of chamber maintenance practices. It is emerging as a game-changer in the biopharma industry, particularly for the ROI it offers facility managers.
Three Key Benefits of Predictive Chamber Maintenance
The decision to incorporate predictive maintenance practices requires a clear understanding of how this strategy can affect the facilities’ bottom line and comply with their sustainability goals.
Benefit 1: Operational Cost Savings
Implementing predictive maintenance directly reduces costs across multiple areas of biopharma storage operations.
- Reduced expenditures through targeted repairs: Rather than performing costly emergency repairs after a failure, predictive tools allow for proactive identification of threatening issues. By addressing small issues before they manifest into big ones, expensive emergency breakdowns (that often occur outside normal business hours) can be avoided.
- Extended lifespan of equipment: Acting on predictive insights helps ensure that chambers operate at peak performance, minimizing wear and tear and increasing their efficiency. By extending equipment lifespan, organizations save on capital expenditures by deferring costly replacements.
- Lower insurance premiums: Predictive maintenance practices reduce the risks that lead to chamber failures, product losses, and expensive insurance claims.
- Expert-guided maintenance recommendations: Effective maintenance depends on data insights and expert guidance. Predictive maintenance platforms use AI powered analytics to pinpoint issues and deliver guided recommendations, vastly reducing troubleshooting time.
- Streamlined procurement: Certain replacement parts can have long lead-times and result in costly waiting periods. Armed with precise data, maintenance teams can make compelling cases to accelerate procurement processes and justify ordering necessary spare parts. Having procurement requests backed by actionable insights often results in faster approvals and fewer delays.
Benefit 2: Maximized Uptime Through Increased Efficiency
Operational downtime is a costly challenge for biopharma facilities. Predictive chamber maintenance frees up critical hours by reducing inefficiencies and emergency repairs, enabling teams to work smarter, not longer.
- Real-time chamber analytics: Predictive maintenance allows technicians to precisely detect anomalies in refrigeration systems and make repairs before they affect operating conditions inside the chamber. This reduces the time needed to troubleshoot, locate, and resolve issues.
- Minimize failures: Predictive maintenance prevents unscheduled breakdowns, allowing facilities to maintain production schedules, bring products to market, and avoid costly delays in research and aging/progressing stability studies.
- Remote monitoring: Advanced predictive maintenance solutions can monitor sensor data from anywhere, providing deep visibility into refrigeration equipment while reducing the need for on-site supervision. This capability provides flexible options for maintenance teams.
- Risk mitigation: There are 168 hours in a week, but even full-time employees only work about 24% of them. If there is a pending problem with a chamber, it is most likely to manifest outside normal working hours. Predictive tools minimize off-hour disruptions and contribute to higher employee satisfaction and engagement.
- Avoid costly product moves: Unexpected chamber failures can require emergency product moves into backup chambers and worst, making decisions on what products to save or discard due to limited space, putting strain on staff and resources, and creating mountains of paperwork. Predictive tools provide critical data that exposes vulnerabilities in refrigeration equipment so repairs can be made before chamber conditions are adversely affected.
- Reduce operational paperwork: When a failure occurs, current GMP standards require a CAPA (Corrective and Preventive Action) to examine the cause and effect. With predictive maintenance, staff spend significantly less time managing these administrative tasks and investigations, freeing them to focus on higher-value activities.
Benefit 3: Risk Mitigation
The financial and reputational risks of compromised biopharma products can be devastating. Predictive chamber maintenance mitigates these risks by ensuring that operations are secure and reliable.
- Prevent product loss: Product loss resulting from chamber failures can cost upwards to millions of dollars per occurrence. Predictive capabilities safeguard stored high-value products by addressing risks proactively before they impact product integrity.
- Compliance assurance: Biopharma storage facilities must adhere to stringent regulatory guidelines. Predictive maintenance tools help meet and exceed regulatory standards by ensuring chambers always operate within required specifications, avoiding penalties and audits from avoidable failures.
- Reputation protection: Businesses that demonstrate operational excellence and sustainability programs build trust with their partners and customers and gain a positive reputation in the industry as a dependable forward-thinking organization.
Quantifying ROI in Predictive Maintenance
Determining an exact dollar value will depend on an organization’s unique circumstances, but even conservative projections reveal significant benefits across key areas, such as cost savings, speed to market, reduced downtime, and employee efficiencies.
To assess the potential ROI of predictive chamber maintenance, biopharma facility managers need to ask themselves the following questions:
- What more productive tasks could my team focus on?
- Is my team relying on tribal knowledge?
- How much could be saved if our equipment’s lifespan increased by five or more years?
- What was the downtime cost of our last major chamber failure? If any product was lost, how much did that cost?
- How many hours and dollars have we spent on investigations and documentation for unplanned repairs?
- How much could we save by employing predictive analytics and sustainability practices, and getting products to market faster?
By addressing these questions, biopharma facilities can assemble a very compelling business case for the pros of incorporating predictive maintenance practices.
Implementation in Biopharma Operations
In the biopharma industry, predictive maintenance solutions do more than just save costs and time. They allow maintenance teams to focus on their core mission — ensuring business continuity and product safety. It also allows investments in innovation that delivers better results for customers.
By minimizing failures, reducing downtime, and safeguarding high-value product, this approach offers financial stability, operational excellence and sustainability in a rapidly evolving industry. Implementing predictive maintenance is not only a smart investment for biopharma facilities but also a critical step towards ensuring the quality and reliability of life-saving products for patients in need.
Granted, the transition to predictive chamber maintenance requires initial investment and training, but the long-term ROI far outweighs the upfront costs. Many companies are able to overcome technical and cultural barriers through a phased implementation process, starting with their high-impact assets before scaling out globally.
This is Pharma 4.0
Predictive maintenance represents an unmatched shift towards operational consistencies and efficiencies. It enables facility managers to move from reactive firefighting to proactive asset optimization. Its ability to deliver cost savings, ensure compliance, and protect high-value product indicates that incorporating predictive maintenance is not only a necessity for operational excellence and sustainable practices, but also a significant driver of competitive advantage. It’s Pharma 4.0, and like all technological advancements, its adoption into the mainstream is inevitable.
Summary
Predictive chamber maintenance is more than a cost-saving tool — it’s an investment in operational excellence and sustainability. By reducing downtime, streamlining maintenance processes, and protecting critical assets, these solutions empower facilities to stop reacting to chamber failures and start predicting them so they can be prevented.
There are two questions that organizations need to ask themselves, and it’s not whether they can afford to adopt predictive maintenance — but whether they can afford the risks of operating without it. The other is, “What’s the ROI on peace of mind?”